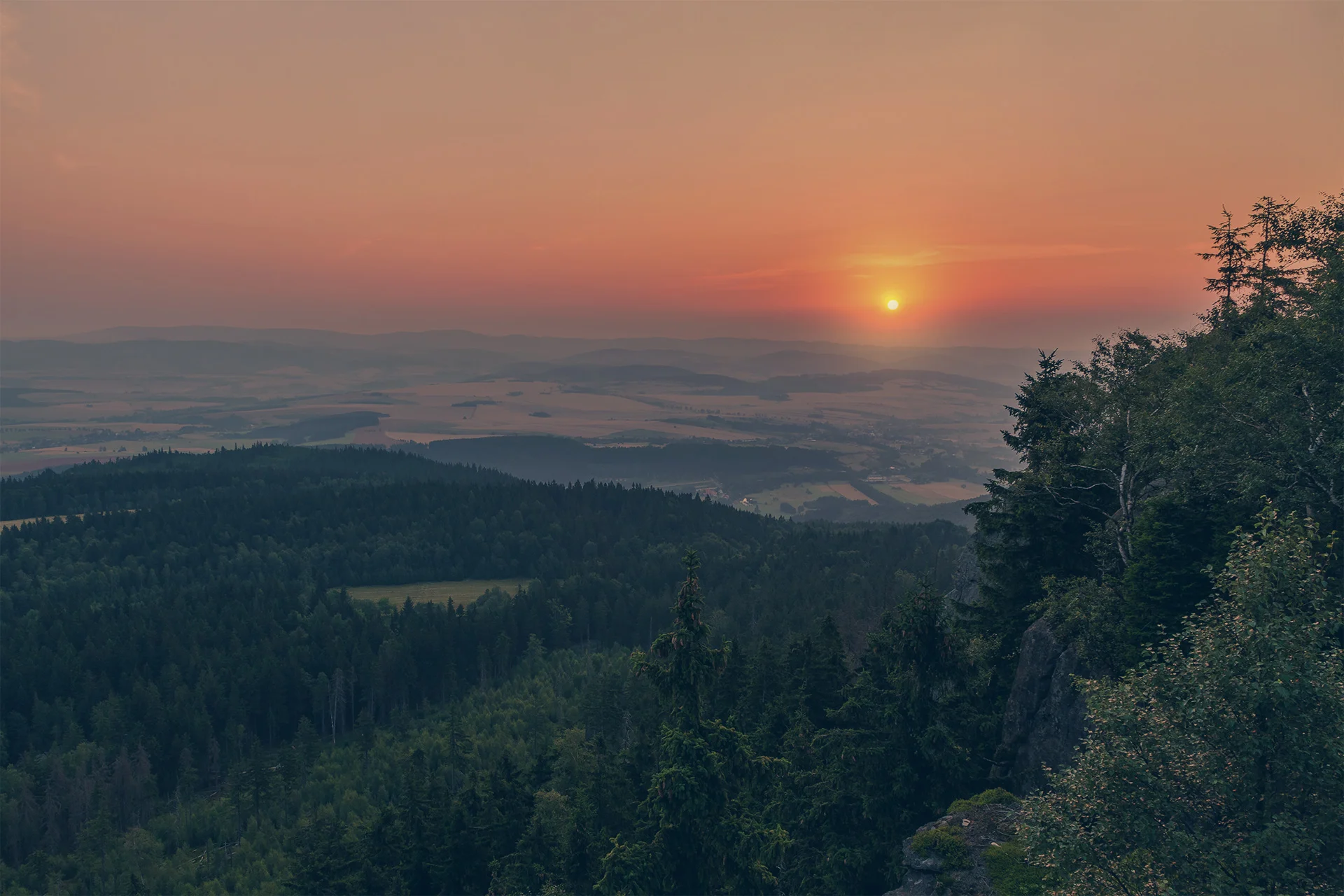
The Alent Dynamic®-method is a proven game changer.
Alent Dynamics® patented automatic dynamic drying process has dried over 190 000 batches and saved more than 500 million kWh of electricity.
Customer example:
OLWO AG, Switzerland
After converting 5 drying chambers to the Alent Dynamic technology, we were able to directly confirm the promised advantages. End cracks are no longer an issue for us and twisting and discoloration have also been greatly improved. We see significant electricity savings and are happy about a more environmentally friendly drying process. The changeover to the Alent Dynamic drying method was very easy and quick in all chambers.
Ueli Lädrach
Head of Operations and Production Olwo AG, Worb
Holzwerke Ladenburger, Germany
Holzwerke Ladenburger is Germany's largest manufacturer of glulam beams, which now installs the new Alent Dynamic® automated wood drying process in 26 of their kilns in their flagship factory Kerkingen. After this they will have the Alent Dynamic® drying process in over 50 kilns at four factories. The purchase is conducted after careful benchmarking against other solutions in the market.
Read more about why Ladenburger invests in automated wood drying process from Alent Dynamic®.

A few of our customers

Testimonials
“With Alent Dynamic Pump technique and soft sensor WMC, we have reduced drying times and got higher accuracy in end moisture content. Good kiln operators and the Alent Academy program is also important factors.”
“Large energy savings and process safety were what made us decide for Alent Dynamic in 2016. In addition to the good drying quality, we are very satisfied with their service. Alent is a valuable partner in wood drying.”
“After testing Alent Dynamic® for 3 months, we ordered 16 additional control systems.”
“The drying time for Douglas fir has decreased by 25% and electricity consumption by 60%
”
“We have seen excellent energy reduction, and reduced quality costs connected to KBS (Kiln Brown Stain).”
“The Alent Dynamic method and their soft sensor for online moisture content are two major technological leaps in wood drying.”
“The result was a higher quality glulam product and higher yield in production. The electricity savings is a bonus, and we are now running Alent systems in 24 kilns. ”
“We see great potential in cooperating with Alent Dynamic for better products and major environmental improvements.”